Trees in savannas often have thick corky bark to insulate the vascular cambium, buds and meristem tissue from fires (PeĢrez-Harguindeguy et al. 2016 ). Outside of fire-prone savannas, bark thickness still varies a lot among species. The English Oak for instance has very thick bark, but doesn’t occur in fire-prone regions. Various theories have been put forward to explain functional variation in bark thickness among species in non-fire-prone ecosystems, like resistance to frost, mechanical stability in windy environments, and buffering against fluctuations in water potential (Rosell et al. 2014 ). Interestingly, it doesn’t look like bark thickness is necessarily associated with other “slow economic” plant traits like thick leaves, wood density and leaf mass per area (Richardson et al. 2015 ). Trees in tropical rainforests often have very thin and smooth bark. It has been suggested that thick bark may be a disadvantage in these ecosystems as it provides shelter for invertebrate enemies (Pausas 2015 ).
In the SECO project , I’m interested in bark thickness as a measure of resistance to fire. Differences in bark thickness might explain variation in carbon dynamics among ecosystems based on their fire regime and tree community composition.
My Dad found some steel pipe that used to be used in the dairy for milk. The pipe had a 23 mm external diameter and a 16 mm internal diameter, meaning the wall thickness was ~7 mm. Punch diameter varies, but 10-15 mm seemed common across the literature I found. The SEOSAW traits manual , originally written by Carla Staver recommends 15 mm. We cut the pipe out using hacksaws, and then cut it into 8 inch lengths. About 1 inch from the top of each section of pipe, I drilled a hole all the way through the pipe. At the other end of the pipe we used a bench grinder to sharpen the pipe, with a bevel on the outside.
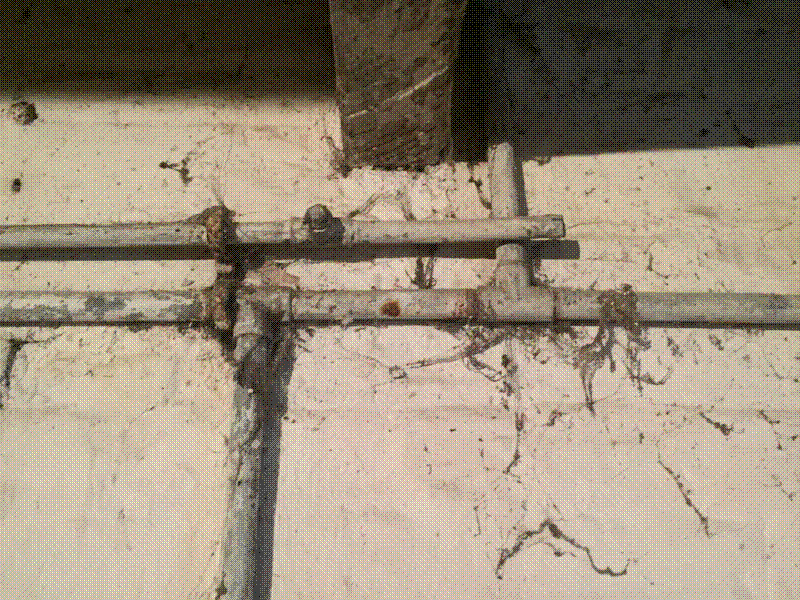
We found some metal rod in the farm buildings attached to a rusting piece of farm machinery called a Lely Cock Pheasant. This machine is also known as a tedder and is used to turn hay, kind of like a mechanised pitchfork. We used an angle grinder to remove the rods, then I cut the rod into 9 inch lengths with a hacksaw, slightly longer than the punch. The rod fits into the drilled hole to use as a handle to pull the bark punch back out of the tree trunk. The rod can also be used to push the bark plug out of the pipe so it can be measured.
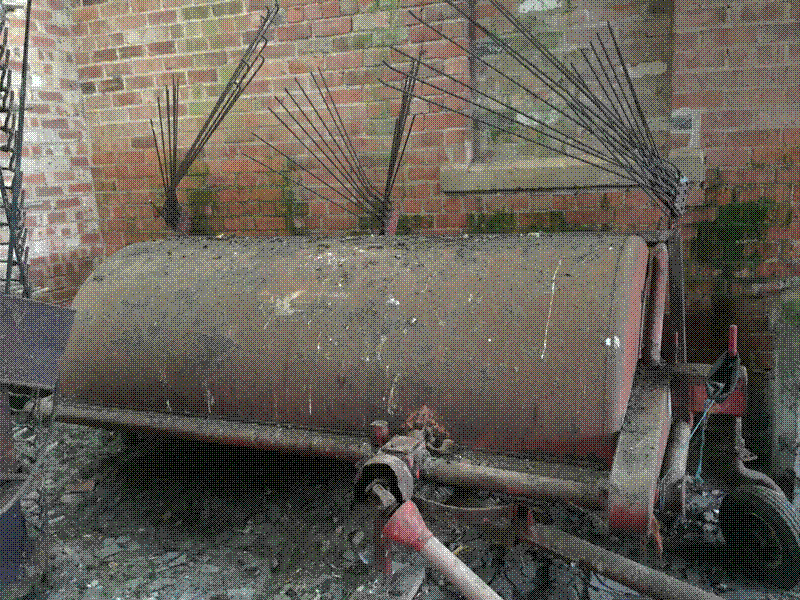
Finally, I cut a small piece of wood to protect the top of the pipe when hammering the pipe into the tree trunk.
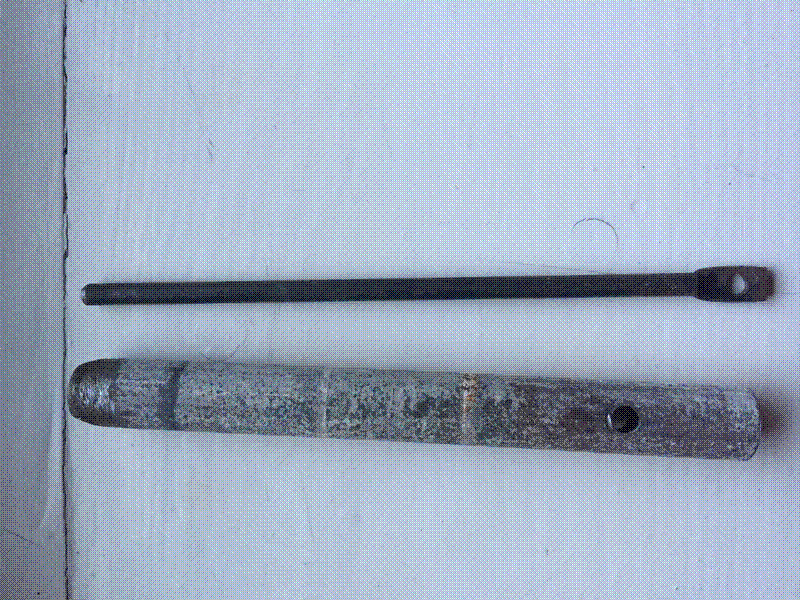
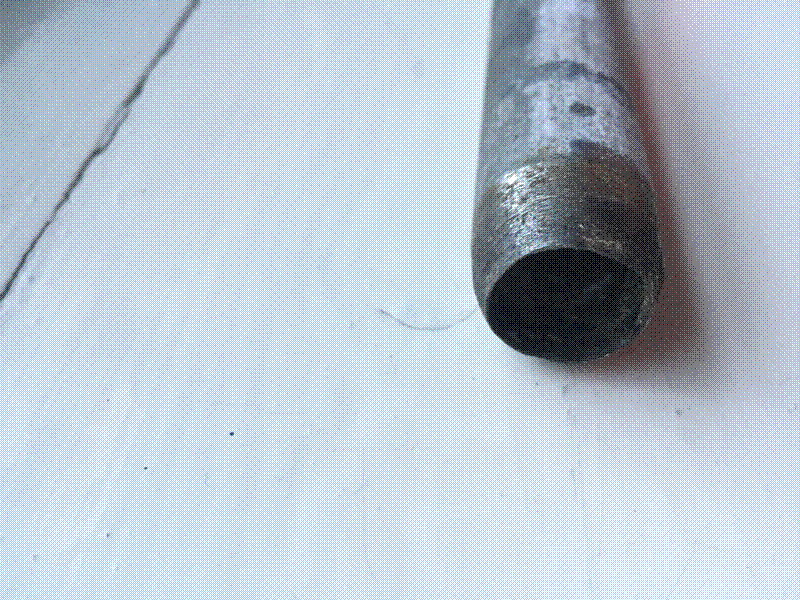
I tested the bark punch on a piece of fresh ash that came down in storm Arwen a few weeks back, fresh enough that I can pretend it’s a living tree trunk. It worked pretty well, though I did notice a couple of nicks where the cutting edge had rolled over. I will reset the angle of the bevel so that it is steeper, and possibly try to temper the metal somehow.
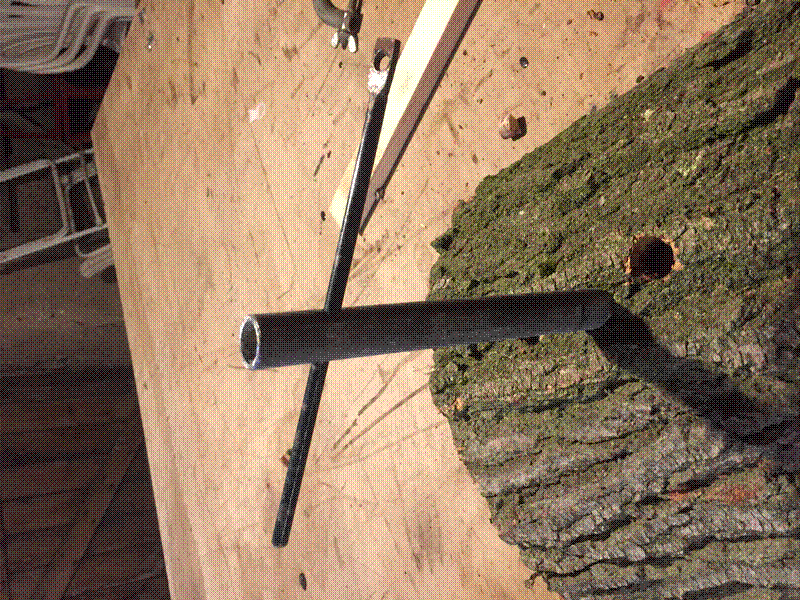
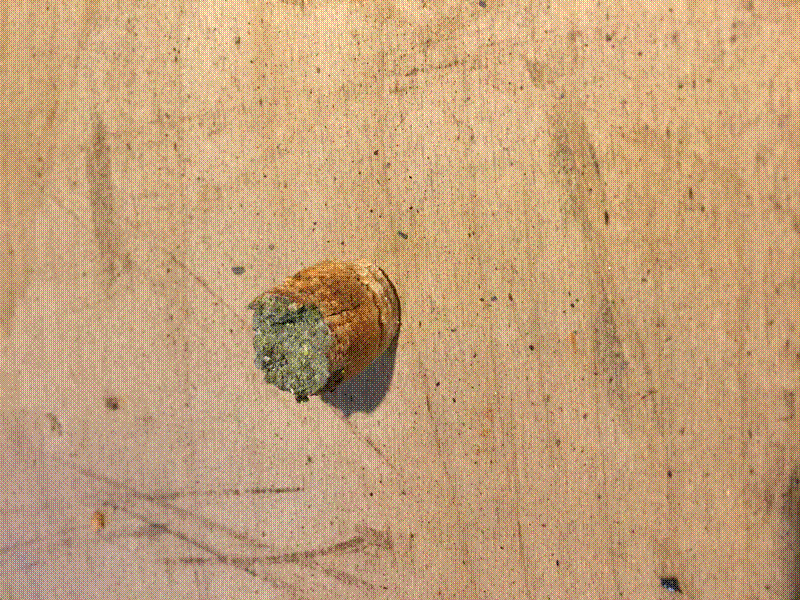
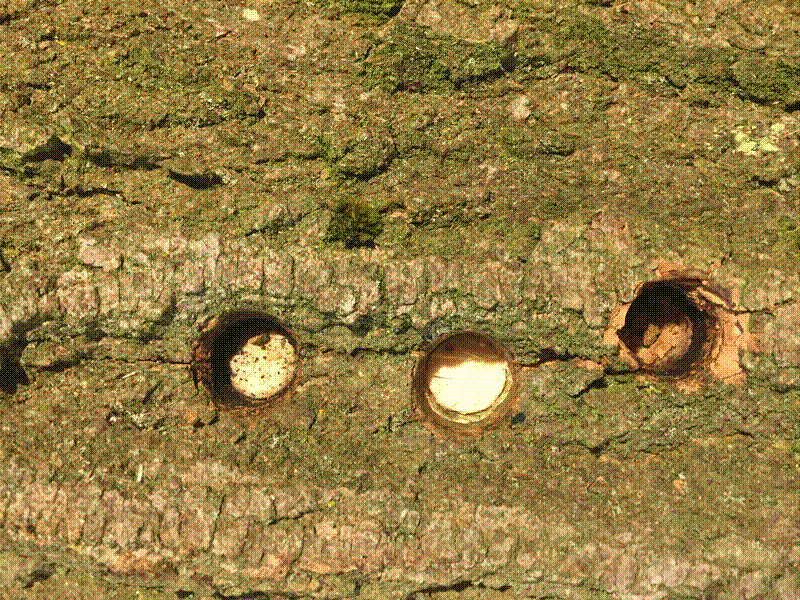